Every decision you make for your transmission rebuild shop should be in favor of reducing risk — both for you and your customers. That's why you use high-quality parts, offer a good warranty, invest in your team's continuing education, and more. You can optimize just about every aspect of your auto shop business, from your workflow to your processes, but what you do next once you've outlined these strategies is crucial: you have to commit to following them. It may sound simple, but ensuring that your team can implement your rebuild process on every single vehicle is a big but important commitment to make.
In order to optimize your rebuild shop for success, you have to find out what processes work for you and then stick to them. In this post, we'll explain why you should always follow a strict transmission rebuild process on every job that comes in the door as well as why consistency is the key to success.
The Benefits of Following A Transmission Rebuild Process
Eliminating the worry of missing a step: When you create a totally personalized rebuild process for your shop, you can practically eliminate the possibility of your tech missing, skipping, or forgetting a step of the process that could lead to failure down the line. By following the listed procedures and turning the same actions into habit, these types of mistakes become far less of a threat to your productivity and profitability. Each rebuild is treated with the same care and attention when you follow the process. Even when distractions or issues arise (which sometimes cannot be avoided), your tech will know exactly where to pick up based on where they left off in the process.
- Staying on time: Following a set rebuild process also allows you to more easily track the amount of time your techs spend (or should be spending) on each step of the process or the rebuild as a whole. Your optimized process can provide timing benchmarks that allow you to estimate when each rebuild will be complete. Not only does this improve your scheduling efficiency, but you'll also be able to more accurately communicate to your customers how long their work will take.
- Reducing comebacks: Perhaps most importantly, when you perfect and implement a strict rebuild process, it's like built-in quality control for your shop. You can ensure that each vehicle gets equal attention and care when your process is as standardized as possible, protecting you from costly mistakes and setbacks that can cause comebacks. Regardless of which tech is on the job or what vehicle they're working on, you can have confidence that your process will get every rebuild done right the first time.
Keep It Consistent for Successful Rebuilds
Creating an optimized transmission rebuild process is only half the work if you really want to decrease risk for your shop and your customers. The true key to success with your process is creating it with consistency in mind and then committing to sticking to it for every possible rebuild. Following your rebuild process means eliminating risky variables that threaten your success. That includes choosing a kit provider that has the quality parts you need for every vehicle (including late models) that comes into your shop as well as specifying the exact series of steps your technicians should follow.
When you eliminate variables, it's easier to pinpoint and solve any rebuilding issues that do arise and threaten to throw your service off course, and it protects your shop's reputation and customer experience from costly slip-ups. When you're ready to take the next step in optimizing your business for success, always look to add consistent providers and processes to your trusted business model.
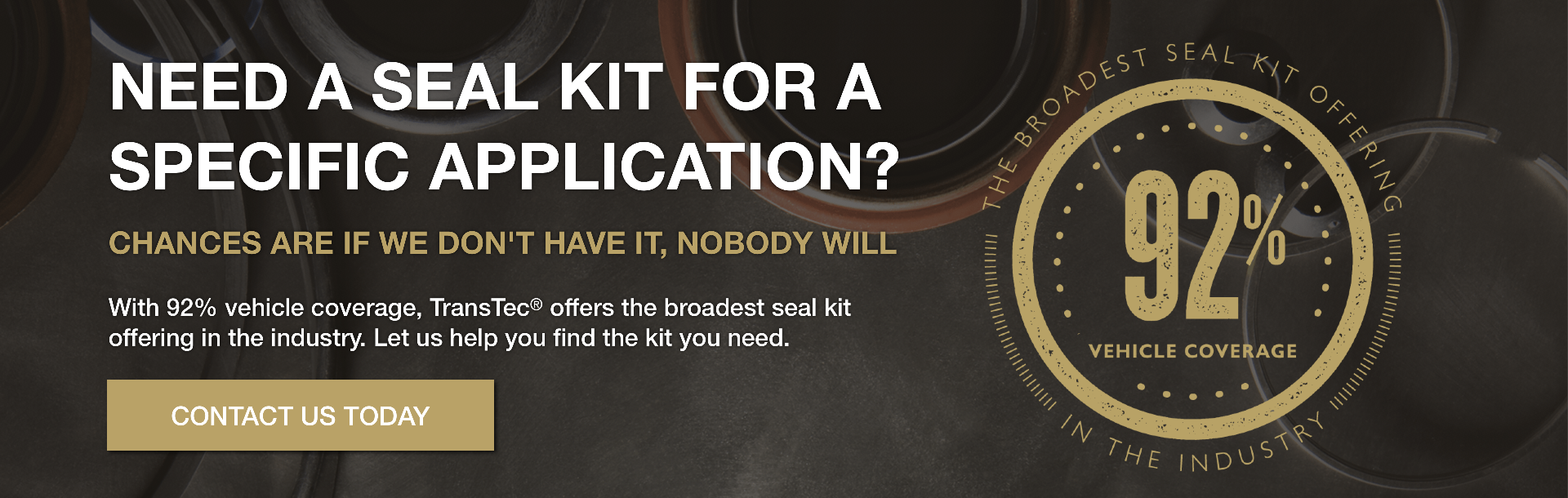